O motor ainda escolhe de maneira autônoma um dos três modos de funcionamento disponíveis: Zero emissão, térmico a gasolina ou misto. A PSA acredita que essa tecnologia híbrida é uma etapa essencial rumo à meta de se fazer um carro que tenha consumo de combustível de 50 km/l.
Mostrando postagens com marcador mecânica. Mostrar todas as postagens
Mostrando postagens com marcador mecânica. Mostrar todas as postagens
18/06/2013
Peugeot Citroën recebeu três prêmios pelo sistema Hybrid Air
A PSA Peugeot Citroën recebeu, na Europa, três prêmios por seu sistema Hybrid
Air, que combina propulsão a gasolina e ar comprimido. Entre os prêmios, estão
“Prêmio das Tecnologias do Futuro MAAF”, o prêmio de inovação “Fleet World
Honours” e o “Engine Technology Development Of The Year”, atribuído à Bosch,
parceira da PSA na tecnologia.
Segundo a fabricante de automóveis, o Hybrid Air é uma tecnologia inédita,
composta por um grupo motopropulsor “full-hybrid”, sem bateria, associando
gasolina e ar comprimido. O conjunto combina um motor a gasolina com uma bomba
hidráulica, armazenamento de energia na forma de ar comprimido e transmissão
automática.
O motor ainda escolhe de maneira autônoma um dos três modos de funcionamento disponíveis: Zero emissão, térmico a gasolina ou misto. A PSA acredita que essa tecnologia híbrida é uma etapa essencial rumo à meta de se fazer um carro que tenha consumo de combustível de 50 km/l.
O motor ainda escolhe de maneira autônoma um dos três modos de funcionamento disponíveis: Zero emissão, térmico a gasolina ou misto. A PSA acredita que essa tecnologia híbrida é uma etapa essencial rumo à meta de se fazer um carro que tenha consumo de combustível de 50 km/l.
16/06/2013
Simulador robótico manipula e controla os comandos de voo
Do lado de fora, ele parece um grande braço robótico industrial segurando um cockpit. Mas, para o piloto dentro do simulador, tudo se parece com uma aeronave real, incluindo as paisagens ao redor e abaixo dele.
Depois que o piloto se senta neste que se tornou o mais moderno simulador de voo do mundo, o braço robótico posiciona-se em um lado da sala cercado de telas de alta definição de todos os lados - incluindo o teto e o chão.
Isso cria um ambiente totalmente imersivo, permitindo que o piloto tenha uma visão completa da paisagem ao redor, incluindo cenas reais de aeroportos.
Quando ele manipula os controles, os comandos de voo são convertidos em movimentos correspondentes do braço robótico em tempo real. Os pilotos geralmente estudam e são treinados em cabines montadas sobre uma plataforma móvel com seis graus de liberdade.
O grande inconveniente destes sistemas é o preço, variando entre 10 e 30 milhões de dólares.
Simulador de voo robótico |
"Um simulador montado em um robô industrial pode reduzir estes custos para cerca de um milhão de euros [US$1,3 mi]", explica Tobias Bellmann, que desenvolveu o simulador robótico com seus colegas Johann Heindl e Olaf Gühring, todos do Centro Aeroespacial Alemão (DLR).
O grande feito do trio foi usar um único braço robótico para implementar o voo de forma interativa.
Isso significa que o piloto não precisa voar em trajetórias predefinidas - ele pode controlar a cápsula do jeito que quiser.
"Para nós, isso significa que os movimentos do braço robótico têm que ser calculados em tempo real - em outras palavras, muito rapidamente - porque não podem ser planejados com antecedência", explica Bellmann.
O simulador também pode funcionar para outros tipos de veículos, incluindo carros e até navios - para isto, basta trocar o software de controle e as cenas projetadas nas telas.
Fonte: Inovação Tecnológica
24/04/2013
Simulador de Soldagem para qualificação profissional
Dados do Mapa do Trabalho Industrial 2012, elaborado pelo Serviço Nacional de Aprendizagem Industrial (Senai), mostra que o Brasil terá de formar 7,2 milhões de trabalhadores em nível técnico e em áreas de média qualificação para atuar no mercado até 2015.
Para atender a essa demanda do setor industrial, a Simulogica - Simulações Computacionais e Sistemas irá desenvolver um simulador de soldagem para qualificação profissional. O projeto foi contemplado pelo edital Senai Sesi Inovação 2012.
Segundo o diretor executivo da empresa, Fabiano Garcia, o simulador constitui-se de um hardware com software embarcado, composto por diversos periféricos que auxiliam seu funcionamento. "Um ambiente virtual tridimensional é utilizado para inserir aluno/aprendiz no processo e simular uma soldagem real", explica.
Garcia afirma que no simulador, o maçarico é adaptado com botões que são integrados com o software através de uma interface eletrônica e um sistema de rastreamento posicional com 6 graus de liberdade, que faz com que o usuário consiga navegar no ambiente virtual. E é esse o grande diferencial do projeto, a simulação realística. "O aluno pode simular todas as situações de aprendizado e treinamento. Ele vivencia em um ambiente simulado as dificuldades e as ações realizadas no mundo real", avalia.
O produto, que será desenvolvido em 2013, é voltado para a qualificação de mão de obra especializada do setor de soldagem, que sofre com a falta de profissionais. "Não temos dúvida no retorno positivo deste novo sistema e nós ainda estaremos contribuindo para a formação de pessoal, treinamento e também na reciclagem destes profissionais", comenta o diretor executivo da Simulogica.
Empresas do setor metalmecânico, naval, petrolífero e automobilístico são as que mais empregam soldadores e devem ser as maiores beneficiadas. Além delas, instituições de treinamento e capacitação profissional também devem fazer uso do produto.
Este é o primeiro produto da Simulogica voltado exclusivamente à indústria. A empresa já desenvolve sistemas de simulação para outras áreas, como segurança, área médica e automobilística.
Para o simulador de soldagem, estima-se um investimento de R$ 300 mil e, segundo Garcia, a expectativa é ter resultados já no segundo semestre de 2013.
Fonte: Karine Wenzel/CIMM
23/04/2013
Usinagem dinâmica diminui consumo de óleo lubrificante
O objetivo da pesquisa era reduzir o consumo de óleo lubrificante pelos motores automotivos. Um motor sem óleo não sobrevive muito tempo. Os pistões exigem uma lubrificação constante, a fim de se moverem com alguma suavidade dentro das camisas no bloco do motor.
Os engenheiros sabem que duas coisas aumentam o nível de fricção em um motor a combustão. A primeira é atribuída à distorção do cilindro onde vai a cabeça do pistão, algo conhecido como distorção estática. A segunda ocorre quando o motor está funcionando e as temperaturas deformam o cilindro. A magnitude dessa distorção térmica depende da temperatura de funcionamento e varia para cada modelo específico de motor.
Apoios indesejados
Na realidade, os pistões não seguem um movimento perfeitamente suave para cima e para baixo - eles tocam o bloco do motor em pontos discretos no interior do cilindro. O resultado é a necessidade de muito mais óleo para lubrificar o motor, além do que o atrito fará com que ele consuma mais combustível.
As montadoras já conseguem compensar a distorção estática. Durante a fase de usinagem final, os técnicos usam uma ferramenta de polimento para simular a cabeça do pistão que será posteriormente montado. Só então o trabalho de acabamento do furo é concluído. A distorção térmica, por outro lado, até hoje não tinha solução, não sendo compensada.
Ferramenta piezoelétrica
Este problema acaba de ser resolvido por pesquisadores do Instituto de Máquinas-Ferramenta e Tecnologia de Formação (IWU), na Alemanha, em colaboração com uma montadora e um fabricante de máquinas-ferramenta.
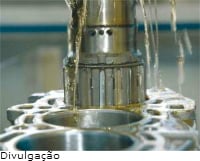
Isto foi possível usando uma ferramenta de polimento capaz de alterar sua própria forma - atuadores piezoelétricos alteram o diâmetro da ferramenta com incrível precisão.
Polimento dinâmico
Os pesquisadores primeiro calculam como o bloco do motor tende a se tornar distorcido: eles determinam o nível de distorção estática tirando a cabeça do cilindro e medindo a extensão em que o furo foi deformado.
A seguir eles simulam a distorção térmica que ocorre em cada modelo de motor utilizando-se de uma temperatura de funcionamento de 90°C como referência.
A nova ferramenta de polir ajusta então sua forma com base nestes cálculos, alterando assim o perfil do furo do bloco do motor de modo que os movimentos do pistão sejam perfeitamente suaves, eliminando o atrito excessivo advindo do seu apoio em poucos pontos no bloco.
Ou seja, não se trata de fazer um furo perfeito, mas de dar ao furo as imperfeições de que ele precisará na prática para que o motor precise de menos lubrificação. E, com menos atrito, ele consumirá menos combustível. O uso da nova ferramenta dinâmica aumentou o tempo de usinagem de cada motor em menos de 30 segundos, o que permite seu uso imediato na linha de produção
26/02/2013
Estudante cria robô controlado via internet
O aluno Rayllonn Nagime, da Escola Técnica Rezende-Rammel, no Rio de Janeiro, criou um robô controlado via internet capaz de reproduzir som e imagem ordenados pelo internauta do local onde estiver.
Nagime conta que a ideia surgiu em um dia em que seu tio não pôde comparecer a uma reunião de família porque estava doente. — A ideia surgiu depois de uma reunião de família em que meu tio não pôde participar. Logo depois desse evento, fui conversando com parentes e amigos e agente chegou a conclusão de que um meio rápido, barato e fácil de as pessoas se comunicarem é a internet. E então veio a ideia de um sistema controlado via internet.
O trabalho de Rayllonn será apresentado na Febrace (Feira Brasileira de Ciências e Tecnologia), feira que estimula a criatividade de estudantes em ciências e engenharia, que acontece entre os dias 12 e 14 de março, na Escola Politécnica da Universidade de São Paulo (USP).
Nagime conta que a ideia surgiu em um dia em que seu tio não pôde comparecer a uma reunião de família porque estava doente. — A ideia surgiu depois de uma reunião de família em que meu tio não pôde participar. Logo depois desse evento, fui conversando com parentes e amigos e agente chegou a conclusão de que um meio rápido, barato e fácil de as pessoas se comunicarem é a internet. E então veio a ideia de um sistema controlado via internet.
Batizado de DroidNet C, o robô-avatar tem uma série de equipamentos e é movido por bateria de carro. Para a caminhada, o projeto conta com esteiras na base. A comunicação à distância é feita através de modem 3G, roteador e wi-fi. O rosto do internauta no avatar é captado pela câmera do computador pessoal e exibida na tela de LCD que serve como cabeça do robô.
Há também um microfone para captar o som do ambiente e caixas de som para reproduzir a voz do controlador. Os olhos do robô são uma câmera instalada no monitor.
Como no filme Avatar, o DroidNet C também é grande: tem quase dois metros de altura e aproximadamente 130 quilos. No entanto, não é preciso entrar em nenhuma cápsula para controlar a máquina — basta um computador, ou até mesmo um smartphone. Nagime conta que também está criando um robô com as mesmas funções, só que menor.
Há também um microfone para captar o som do ambiente e caixas de som para reproduzir a voz do controlador. Os olhos do robô são uma câmera instalada no monitor.
Como no filme Avatar, o DroidNet C também é grande: tem quase dois metros de altura e aproximadamente 130 quilos. No entanto, não é preciso entrar em nenhuma cápsula para controlar a máquina — basta um computador, ou até mesmo um smartphone. Nagime conta que também está criando um robô com as mesmas funções, só que menor.
O trabalho de Rayllonn será apresentado na Febrace (Feira Brasileira de Ciências e Tecnologia), feira que estimula a criatividade de estudantes em ciências e engenharia, que acontece entre os dias 12 e 14 de março, na Escola Politécnica da Universidade de São Paulo (USP).
30/01/2013
Sistema de classes dos parafusos de aço inoxidável
SISTEMA DE DESIGNAÇÃO DE CLASSES
A propriedade característica do aço inoxidável austenítico é que, diferentemente do aço carbono, ele não pode ser endurecido por tratamento térmico, mas somente por deformação a frio. Por este processo, o aço inoxidável austenítico tem suas propriedades mecânicas aumentadas consideravelmente.
Os materiais A1, A2 e A4 são divididos em três classes cada um: 50 - 70 - 80, dependendo do método de produção e dimensões.
O número da classe exprime 1/10 da resistência à tração em N/mm². Assim a classe 80 tem uma resistência à tração mínima de 800 N/mm².
Classe 50 - Material mole obtido por deformação a quente e raramente utilizado na fabricação de fixadores.
Classe 70 - A classe mais comumente usada para todos os fixadores deformados a frio.Esta é a classe padrão e a normalmente fornecida, a não ser que haja especificação em contrário por parte do cliente
Classe 80 - A classe com maiores propriedades mecânicas devido a uma deformação extra a frio que coloca o material ao nível aço carbono 8.8, tornando-os assim intercambiáveis, sem a necessidade de qualquer adaptação.
![]() |
Parafuso classe A2 - 70 |
AÇO INOXIDÁVEL
|
PARAFUSOS
|
PORCAS
| |||||
grupo
|
material
|
classe
|
diâmetro
d
|
resistência à
tração
Rm 2)
N/mm², min.
|
limite de escoamento
de 0,2%
Rp0,2 2)
N/mm², min.
|
alongamento
Al 3)
mm, min
|
carga de prova
Sp
N/mm²
|
50
|
M39
|
500
|
210
|
0,6d
|
500
| ||
austenítico
|
A1, A2, A4
|
70 1)
|
M20
|
700
|
450
|
0,4d
|
700
|
M20 / M30
|
500
|
250
|
0,4d
|
500
| |||
80 2)
|
M20
|
800
|
600
|
0,3d
|
800
|
1) Estes valores se aplicam somente para comprimentos até 8 x d. Nos materiais A2 e A4 a classe mais comum é a 70.
2) Valores calculados em termos da área da rosca onde é aplicada a carga de tração.
3) O alongamento na fratura deve ser determinado no próprio parafuso com comprimento 3 x d e não em corpo de prova preparado.
2) Valores calculados em termos da área da rosca onde é aplicada a carga de tração.
3) O alongamento na fratura deve ser determinado no próprio parafuso com comprimento 3 x d e não em corpo de prova preparado.
Resistência à tração é a relação entre a máxima carga de tração aplicada e a área original da secção transversal do material.
Limite de escoamento é a carga de tração na qual deixa de existir proporcionalidade entre a carga aplicada e a deformação ocorrida.
Limite de escoamento de 0,2% é utilizado para classes de resistência maiores onde o limite de escoamento convencional é difícil der ser determinado, e é a carga de tração na qual, após o cessamento da mesma, o material apresenta uma deformação plástica de 0,2%.
Alongamento é a variação do comprimento original do corpo de prova, após a fratura ocorrida no teste de tração. Normalmente é expresso em valor percentual.
Carga de Prova é uma carga pré-determinada, geralmente um múltiplo da carga de serviço, à qual o material é submetido antes de ser admitido para uso.
Fonte: Dapco - Fixadores Inoxidáveis
15/01/2013
Nissan vai lançar carro com direção eletrônica
A montadora japonesa Nissan anunciou que vai lançar em 2013 o primeiro carro com a tecnologia steer-by-wire. Em lugar de conectar o volante às rodas por meio de uma ligação mecânica - a famosa barra de direção - no novo sistema o comando é transmitido do volante para as rodas eletronicamente. Nas rodas, os comandos são interpretados e usados para acionar motores elétricos que fazem as rodas virarem ou retornarem à posição original. Segundo a empresa, o sistema transmite a intenção do motorista para as rodas a uma velocidade superior à da conexão mecânica.
O próprio sistema se encarrega de fazer pequenos ajustes nas rodas em decorrência de irregularidades no piso, além de deixar o motorista livre das trepidações no volante. A direção eletrônica conta ainda com a ajuda extra de uma câmera, instalada à frente do espelho retrovisor interno, que auxilia o motorista a manter o carro estável na rota, evitando que ele dance na pista por movimentos sutis no volante.
Segundo a Nissan "esse sistema é uma inovação em termos mundiais, uma tecnologia que melhora a estabilidade do veículo fazendo pequenos ajustes de ângulo, de forma que o veículo monitora a via para manter-se na faixa em que está viajando". O sistema também consegue anular balanços no carro gerados por ventos laterais, naturais ou gerados pela passagem de outros carros. Tudo é feito automaticamente, sem que o motorista sinta no volante os ajustes que o sistema vai fazendo nas rodas.
O sistema eletrônico possui três unidades de processamento e um sistema de detecção de falhas que passa automaticamente o controle para o próximo processador se houve alguma falha naquele que estiver controlando a direção. Se a bateria falhar, e todo o sistema eletrônico deixar de funcionar, uma "embreagem" mecânica conecta o volante às rodas - um sistema parecido com os freios de elevadores -, e o carro passa a ser dirigido mecanicamente, na forma tradicional.
Embora dê segurança ao motorista, o sistema de backup mecânico aumenta o peso do conjunto, eventualmente anulando os ganhos de economia de combustível que o sistema deve proporcionar. Mas, na avaliação da empresa, é importante para que os consumidores ganhem confiança na tecnologia. A direção eletrônica, ou steer-by-wire, é parte do conceito drive-by-wire, onde todos os comandos do carro passam a ser feitos eletronicamente.
O sistema anula balanços no carro gerados por ventos laterais e por irregularidades na pista, sem que o motorista sinta nada no volante.[Imagem: Nissan/SIT]
Fonte: Site Inovação Tecnológica
05/12/2012
Características e classificação dos Aços
São os materiais metálicos quantitativamente mais empregados na indústria. São ligas ferro-carbono, podendo ter elementos de liga adicionados propositadamente ou residuais (decorrentes do processo), dependendo das propriedades necessárias. Depois do ferro, o carbono é o elemento mais importante, que é o determinativo do aço. A quantidade de carbono é um dos principais fatores que definem a classificação em aço doce ou duro.Os outros principais elementos de liga encontrados em todos os tipos de aço, em maior ou menor quantidade, são o silício, o manganês, o fósforo e o enxofre. São empregados em equipamentos para a indústria mecânica, como em veículos de transporte de toda natureza, aparelhos elétricos e eletrônicos, eletrodomésticos e em máquinas em geral, além de ter grande aplicação na construção civil.
Chamado também de aço especial - o aço liga - é composto de uma liga de ferro-carbono com elementos de adição (níquel, cromo, manganês, tungstênio, molibdênio, vanádio, silício, cobalto e alumínio) para conferir a esse aço características especiais, tais como: resistência à tração e à corrosão, elasticidade e dureza, entre outras, tornando-os melhores do que os aços-carbono comuns.
A adição de elementos de liga tem o objetivo de promover mudanças microestruturais que, por sua vez, promovem mudanças nas propriedades físicas e mecânicas, permitindo que ao material desempenhar funções específicas.
Os aços-liga costumam ser designados de acordo com os elementos predominantes, como, por exemplo, aço-níquel, aço-cromo e aço-cromo-vanádio. Seguem a mesma classificação dos aços-carbono, dividindo-se também em graus, tipos e classes. Os sistemas de classificação também são os mesmos, destacando-se os sistemas SAE, AISI, ASTM e UNS.
Os aços-liga podem ser encontrados em praticamente todos os segmentos industriais, desde a construção civil até a construção naval, passando pelas indústrias petrolífera, automobilística e aeronáutica.
Aços de alta liga são aqueles cuja soma dos elementos ultrapassa 5%. Três grupos podem representar os aços ligados: aços temperados e revenidos, aços tratáveis termicamente e aços resistentes à corrosão e ao calor.
10xx - aços-carbono;
11xx - aços-carbono com muito enxofre e pouco fósforo;
12xx - aços-carbono com muito enxofre e muito fósforo;
13xx - manganês (1,75%);
23xx - níquel (3,5%);
25xx - níquel (5%);
31xx - níquel (1,5%), cromo (0,6%);
33xx - níquel (3,5%), cromo (1,5%);
40xx - molibdênio (0,2 ou 0,25%);
41xx - cromo (0,5; 0,8 ou 0,95%), molibdênio (0,12; 0,2 ou 0,3%);
43xx - níquel (1,83%), cromo (0,5 ou 0,8%), molibdênio (0,25%);
44xx - molibdênio (0,53%);
46xx - níquel (0,85 ou 1,83%), molibdênio (0,2 ou 0,25%);
47xx - níquel (1,05%), cromo (0,45%), molibdênio (0,25%);
48xx - níquel (3,50%), molibdênio (0,25%);
50xx - cromo (0,28% ou 0,40%);
51xx - cromo (0,80, 0,90, 0,95, 1,00 ou 1,05%);
61xx - Cromo (0,80 ou 0,95%), vanádio (0,10 ou 0,15%);
86xx - Níquel (0,55%), cromo (0,50 ou 0,65%), molibdênio (0,20%);
87xx - Níquel (0,55%), cromo (0,50%), molibdênio (0,25%);
92xx - Manganês (0,85%), silício (2,00%);
93xx - Níquel (3,25%), cromo (1,20%), molibdênio (0,12%)
94xx - Manganês (1,00%), níquel (0,45%), cromo (0,40%), molibdênio (0,12%);
97xx - Níquel (0,55%), cromo (0,17%), molibdênio (0,20%);
98xx - Níquel (1,00%), cromo (0,80%), molibdênio (0,25%);
Os dois números representados pelas letras "xx" indicam a quantidade de carbono do aço. Por exemplo: o aço 1020 apresenta 0,2% de carbono.
Os aços que possuem requisitos de temperabilidade adicionais recebem um H após a sua classificação.
Chamado também de aço especial - o aço liga - é composto de uma liga de ferro-carbono com elementos de adição (níquel, cromo, manganês, tungstênio, molibdênio, vanádio, silício, cobalto e alumínio) para conferir a esse aço características especiais, tais como: resistência à tração e à corrosão, elasticidade e dureza, entre outras, tornando-os melhores do que os aços-carbono comuns.
A adição de elementos de liga tem o objetivo de promover mudanças microestruturais que, por sua vez, promovem mudanças nas propriedades físicas e mecânicas, permitindo que ao material desempenhar funções específicas.
Os aços-liga costumam ser designados de acordo com os elementos predominantes, como, por exemplo, aço-níquel, aço-cromo e aço-cromo-vanádio. Seguem a mesma classificação dos aços-carbono, dividindo-se também em graus, tipos e classes. Os sistemas de classificação também são os mesmos, destacando-se os sistemas SAE, AISI, ASTM e UNS.
Os aços-liga podem ser encontrados em praticamente todos os segmentos industriais, desde a construção civil até a construção naval, passando pelas indústrias petrolífera, automobilística e aeronáutica.
Aços de alta liga são aqueles cuja soma dos elementos ultrapassa 5%. Três grupos podem representar os aços ligados: aços temperados e revenidos, aços tratáveis termicamente e aços resistentes à corrosão e ao calor.
O AISI (American Iron Steel Institute) é o sistema americano para a classificação dos aços. Na prática, o sistema de classificação mais adotado é o SAE-AISI. Nele, o aço carbono é identificado pelo grupo 1xxx.
Os algarismos base para os vários aços-carbono e aços ligados e as porcentagens aproximadas dos elementos de liga mais significativos recebem classificação da seguinte forma:
Os dois números representados pelas letras "xx" indicam a quantidade de carbono do aço. Por exemplo: o aço 1020 apresenta 0,2% de carbono.
Os aços que possuem requisitos de temperabilidade adicionais recebem um H após a sua classificação.
04/12/2012
Laboratório Brasileiro de Excelência em Tecnologia de Soldagem
A Petrobras assinou na última terça-feira (27) termo de cooperação com o Senai, no valor de R$ 11,5 milhões, para implantação do Laboratório Brasileiro de Excelência em Tecnologia de Soldagem, no Rio de Janeiro (RJ). A estrutura atenderá às necessidades de pesquisa, desenvolvimento e qualificação de processos da área e será o primeiro laboratório deste tipo na América Latina.
O investimento em processos de soldagem caracteriza um avanço para a implantação de projetos do segmento de petróleo, já que a atividade é considerada essencial em diversas obras em construção no Brasil. As tecnologias desenvolvidas no laboratório contribuirão para o aumento da produtividade, impactando positivamente os custos e a entrada em operação de empreendimentos.
A infraestrutura inclui processos robotizados e tecnologia a laser que permitem desenvolver conhecimentos e técnicas inéditas de soldagem e montagem para dutos, equipamentos e chapas. Tais recursos possibilitarão ao Senai se posicionar entre os mais conceituados laboratórios de soldagem do mundo e dar suporte às demandas do mercado de óleo e gás com soluções antes desenvolvidas fora do país. Além disso, será possível multiplicar os conhecimentos acumulados com a formação de mão de obra especializada, cada vez mais demandada pelo mercado nacional.
![]() |
O termo de cooperação tem duração de 36 meses. |
Integrante do Programa Tecnológico de Transporte (Protran), da Petrobras, o laboratório será instalado no Centro de Tecnologia Senai Solda, no Maracanã. O início das atividades está previsto para o primeiro semestre de 2013. O termo de cooperação tem duração de 36 meses.
Fonte: Assessoria de imprensa
26/11/2012
Cresce a tendência da aplicação do alumínio na fabricação de motores
A tendência da indústria automotiva é utilizar cada vez mais alumínio na fabricação de todo o motor (cabeçote, bloco e cárter), uma vez que o metal mais leve ajuda a reduzir o peso do veículo, que a cada dia passa a agregar mais conteúdo, seja por questões de segurança (como a obrigatoriedade do air bag e freios ABS, em 2014), ou por motivos de conforto.
Redução de peso garante economia de combustível e menor índice de emissões de CO2, e favorece a performance do torque e a potência dos veículos, mas a leveza do alumínio não é a única vantagem do metal na fabricação de componentes automotivos.
Com o alumínio nos motores, em substituição ao ferro fundido, o comportamento acústico e térmico é superior (uma vez que possui maior capacidade de absorção de ruídos e vibrações, e de dissipação do calor), e há ganhos de agilidade e de melhoria nos processos produtivos, pois é possível produzir peças de maior complexidade construtiva, precisão dimensional e melhor usinabilidade, não havendo a necessidade de pintura ou outros tratamentos de superfície, gerando economia e permitindo melhor acabamento superficial com excelente resistência à corrosão.
Outro benefício do alumínio é o fato de ser 100% reciclável, infinitas vezes e a baixo custo, apresentando ainda elevado valor residual. Assim, blocos de motor fabricados em alumínio oferecem menor impacto ambiental que os produzidos com ferro fundido.
Porém, todo benefício tem um custo e a diferença de preço entre o alumínio e o ferro fundido muitas vezes norteou as montadoras nacionais pela opção mais barata, o ferro fundido, principalmente nos modelos de menor valor agregado, como os veículos compactos populares.
A Peugeot quebrou este paradigma com o 207, ao entregar ao consumidor um veículo compacto com motor 1.4 l, 100% em alumínio. Outro compacto que segue esta mesma linha, porém de segmento mais elevado, é o Citroën C3.
Para reforçar este coro, a Toyota optou em utilizar o metal no Etios, o primeiro veículo compacto popular da montadora no Brasil, que utiliza motores com bloco, cabeçote e carter de alumínio. São propulsores 1.3l e 1.5l, que equipam duas versões do Etios, hatchback e sedã. Em tempo, a Toyota aplica alumínio nos motores 1.8l e 2.0l que equipam o sedã médio Corolla, produzido em Indaiatuba (SP) desde 1998.
A proposta da Toyota é comercializar 70 mil unidades do Etios por ano e, com as projeções de mercado sempre em alta, decidiu investir em uma fábrica de motores no município de Porto Feliz (SP), onde fará, a partir de 2015, os propulsores 1.3l e 1.5l do Etios, e os 1.8l e 2.0l do Corolla, com uma capacidade anual prevista de cerca de 200.000 unidades.
De acordo com o diretor comercial da Metalur e Tecal Alumínio, Luiz Alberto Lopes, os motores da Toyota serão fundidos internamente. “Tal como faz a Honda para quem fornecemos metal líquido”, comenta. Além de fornecer para Honda, a Metalur também abastece a Magal, que produz blocos de alumínio para a PSA - Peugeot Citroën, e parte do metal utilizado pela Nemak, que funde blocos de alumínio para a Ford.
A tendência, segundo Lopes, de consumo do alumínio para fabricação de motores no Brasil é de crescimento. “Em 3 a 4 quatro anos acredito que todas as montadoras deixarão de usar o ferro fundido e passarão a utilizar o alumínio”, comenta o executivo, ao explicar que o maior incentivo é a conquista dos índices de eficiência energética e, consequentemente, emissões de gases. “A produção brasileira de blocos de alumínio ainda é pequena se comparada com o volume de veículos leves comercializados, assim, ainda há espaço para triplicar o consumo do metal”, avalia.
Lopes comenta ainda que outras montadoras também tem planos de iniciar a produção de motores com cabeçote e bloco de alumínio, como a Nissan, que em breve deve inaugurar uma nova planta em Resende (RJ).
Já a General Motors deve estar com sua nova fábrica de motores em Joinville (SC) funcionando com capacidade total, que significa produção de 120 mil blocos e 200 mil cabeçotes por ano, até o final de 2013. Os componentes irão abastecer as plantas de Gravataí (RS) e Rosário, na Argentina. De acordo com informações do site Auto Segredos, blocos e cabeçotes serão confeccionados em alumínio.
Apesar de a GM não comentar oficialmente o fato, rumores dão conta de que lá serão produzidos três motores: 1.2l S-TEC II, o 1.6l 16v Ecotec e o 1.8l 16v Ecotec. O primeiro não existe em nenhum modelo no Brasil, mas aplicado no Chevrolet Aveo, feito na Coréia do Sul, que por aqui é chamado de Chevrolet Sonic, e vem com o motor Ecotec 1.6l 16v, que tem apenas o cabeçote e o cárter em alumínio, sendo o bloco em ferro fundido.
O mesmo ocorre com o motor 1.8l 16v Ecotec que equipa os Chevrolet Cruze e Cruze Sport6 (cabeçote e cárter em alumínio e bloco em ferro fundido). Assim, se as informações estiverem corretas, tudo leva a crer que em breve Sonic e Cruze terão upgrade em termos de motorização.
Fato é que o uso do alumínio em blocos de motores não é uma novidade, uma vez que Honda, Peugeot, Citroën e mais recentemente a Ford investiram na produção de propulsores 100% em alumínio.
A Honda utiliza alumínio como matéria-prima dos motores desde 2008, na planta em Sumaré (SP). Antes disso, em 2004, a Peugeot passou a fabricar em Porto Real (RJ) motores 1.4l com bloco de alumínio, e mais recentemente, em 2010, foi a vez da Ford investir em blocos de alumínio, na fábrica em Taubaté, onde produz o Sigma 1.6l.
Fonte: Aluauto, com adaptações.
05/11/2012
O que é Revenimento?
Revenimento é o tratamento térmico que se faz nos aços já temperados, com a finalidade de diminuir a sua fragilidade, isto é, torná-lo menos quebradiço.
O revenimento é feito aquecendo-se a peça temperada até uma certa temperatura resfriando-a em seguida. As temperaturas de revenimento são encontradas em tabelas e para os aços ao carbono variam entre 210 ºC e 320 ºC.
Fases do Revenimento:
1ª Fase – Aquecimento:
Feito geralmente em fornos controlando-se a temperatura com pirômetro. Nos pequenos trabalhos o aquecimento pode ser feito apoiando-se a peça polida, em um bloco de aço aquecido ao rubro.
O forte calor que desprende do bloco, aquece lentamente a peça, produzindo nesta uma coloração que varia à medida que a temperatura aumenta. Essas cores, as quais possibilitam identificar a temperatura da peça, são denominadas cores de revenimento.
Tabela de cores de revenimento dos aços ao carbono:
- Amarelo claro 210 ºC
- Castanho avermelhado 270 ºC
- Amarelo palha 220 ºC
- Violeta 280 ºC
- Amarelo 230 ºC
- Azul escuro 290 ºC
- Amarelo escuro 240 ºC
- Azul marinho 300 ºC
- Amarelo ouro 250 ºC
- Azul claro 310 ºC
- Castanho claro 260 ºC
- Azul acinzentado 320 ºC
2ª Fase – Manutenção da Temperatura:
Possível quando o aquecimento é feito em fornos.
3ª Fase – Resfriamento:
O resfriamento da peça pode ser:
Lento –> deixando-a esfriar naturalmente.
Rápido –> mergulhando-a em água ou óleo.
Efeitos do revenimento
Diminui um pouco a dureza da peça temperada, porém aumenta consideravelmente a sua resistência aos choques. Geralmente, toda peça temperada passa por um revenimento, sendo até comum dizer "peça temperada" ao invés de "peça temperada e revenida".
01/11/2012
O que é têmpera?
Têmpera é o tratamento térmico aplicado aos aços com porcentagem igual ou maior do que 0,4% de carbono. O efeito principal da têmpera em um aço é o aumento da dureza.
Fases da têmpera:
1ª Fase – Aquecimento:
A peça é aquecida em forno ou forja, até uma temperatura recomendada. (Por volta de 800 ºC para os aços ao carbono).
2ª Fase – Manutenção da temperatura:
Atingida a temperatura desejada esta deve ser mantida por algum tempo afim de uniformizar o aquecimento em toda a peça.
3ª Fase – Resfriamento:
A peça uniformemente aquecida na temperatura desejada é resfriada em água, óleo ou jato de ar.
Efeitos da Têmpera:
1 - Aumento considerável da dureza do aço.
2 - Aumento da fragilidade em virtude do aumento de dureza. (o aço torna-se muito quebradiço). Reduz-se a fragilidade de um aço temperado com um outro tratamento térmico denominado revenimento.
Observações:
1 - A temperatura da têmpera é conferida em tabelas específicas.
2 - O controle da temperatura durante o aquecimento, nos fornos, é feito por aparelhos denominados pirômetros. Nas forjas, o mecânico identifica a temperatura pela cor do material aquecido.
3 - De início o aquecimento deve ser lento, (pré-aquecimento),afim de não provocar defeitos na peça. 4 - A manutenção da temperatura varia de acordo com a forma da peça; o tempo nesta fase não deve ser além do necessário.
Assinar:
Postagens (Atom)
Marcadores
engenharia
(604)
mecânica
(315)
tecnologia
(211)
ciências
(188)
notícias
(133)
automação
(100)
eletricidade
(98)
cursos técnicos
(87)
administração
(39)
refrigeração
(37)
astronomia
(34)
concursos
(25)
segurança do trabalho
(12)
os cientistas
(4)
mulheres cientistas
(3)
As Dez Mais Lidas...
-
ESCALA NATURAL Escala natural é aquela utilizada quando o tamanho do desenho do objeto é igual ao tamanho real do mesmo, isto é, do mes...
-
[1] O sistema CONFEA/CREA enuncia as condutas esperadas para a boa prática da Engenharia. O objetivo do CONFEA é controlar o exercício da en...
-
100% DE ACERTOS 1) O conceito de desenvolvimento sustentável dita acerca da compatibilização das variáveis ambientais, sociais e econômica...
-
[1] A região gráfica para o desenho de objetos do AutoCAD é um plano cartesiano X e Y, sendo usado para localizar um ponto na tela. Existem ...
-
1) Na legenda de desenho técnicos são encontradas duas figuras que representam o método de projeção ortográfica e para a sua elaboração são ...
-
Conexões industriais são os meios utilizados para unir tubulações a outras tubulações e a equipamentos, como: trocadores de calor, vasos de...
-
[1] O objetivo da pesquisa qualitativa é a descrição completa e detalhada do objeto de estudo, para entender razões e motivações, e o que to...
-
1) Um Plano de Gerenciamento de Resíduos Sólidos (PGRS) bem implementado traz para a instituição os conceitos de sustentabilidade tão em evi...
-
1) Para um conjunto ser um espaço vetorial, ele deve satisfazer oito propriedades; e que para um conjunto não ser um espaço espaço veto...
-
Questionário 01 Pergunta 1 As obras de arte consistem em estruturas responsáveis por transpor obstáculos, dando continuidade a uma deter...
Leia também...
PORTFÓLIO - Química e Ciências dos Materiais [NOTA MÁXIMA]
Relatório de Aula Prática - Química e Ciências dos Materiais Observar por meio de alguns testes de propriedades físicas o comportamento do...
